ACwiki技術部見習い活動(仮)
「アリシアたんを自律制御させてみたい」
第6話 〜アリシアたん(?)フレーム製作〜
■ past ■ up ■ future ■
■ 0.序論
前回作成したそれっぽいモデルですが、
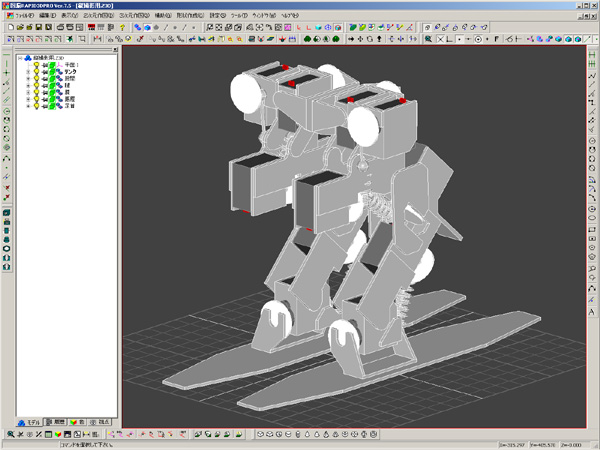
今回はこれを具現化するためにアルミ材を加工しフレームを作製していきます。
しかし、これを書いているのが2012年6月、
思い起こせば前回更新のお知らせをしたのが2011年2月21日の日記で
>ありしあちゃん5話を追加、おそらく1年近く寝ていたかな・・・
今度は1年以上寝てたんだよ!!1123
まあアウトプットが0でないだけマシだと考えることにします。
■ 1.テーマ選定
前回設計したフレームを実際に製作します。
今回の活動も理論や知識は必要ありません・・・
と言いたいところですが、本来は加工技術が必要です。
ただ今回は正直なところ日曜大工だとかD.I.Y.だとか
そのへんのレベルだと思いますので特別解説はしません。
■ 2.現状把握と目標設定
前回設計した以下の材料をまず購入、大まかに切り出しします。
※全てt1.5、外寸
・板材
35×178:2個
25×63:4個
25×45:4個
25×35:4個
25×33:4個
25×23:4個
25×15:2個
・アングル
15×15×12:12個
・深Cチャネル
15×25×54.5:2個
15×25×40:2個
15×25×25:8個
目標は、これらの「板の羅列」を
設計されたフレームという機能性部品にし、
ロボットとして動くよう組み立てることです。
■ 3.活動計画
前回の設計では、肝心なところを全然設計しておらず(笑)、
まずはネジ穴位置等を決定する必要があります。
その後、フレームを大まかに形状出したら、
穴あけ、タップ立てをして
最終的なフレーム形状に仕上げていきます。
今回はオリジナル武装神姫作製に向けたトライアル的な要素も含みますので、
アルマイト処理はその時のお楽しみにとっておきます。
■ 4.要因解析
で、問題は
時間がない
この一点につきます。
そもそも自宅で製作していますので、
使用できる設備が限られています。
ホビー用途といえど動作をする機械部品ですので、
それ相応の精密さも求められます。
■ 5.対策検討と実施
今回特に必要なものは、アルミ素材の形状出しと、
精密な位置での穴あけです。
これらを時間的効率よく行うためには、
加工機の導入が不可欠です。
世界にはさまざまな加工機が存在しますし、
それぞれの加工方法や製作物の種類もさまざまですが、
常套手段となると限られてきます。
今回のアルミの例でいえば、
面加工をするといえばフライス加工、
穴あけ加工をするといえばドリルです。
これらを精密に行うためには、最低でもx−yの移動が可能なテーブルが必要です。
テーブルが複数あっても邪魔なだけですので、
1つのテーブルでフライスもドリルも扱えるとよいでしょう。
そういう考えで主軸に様々な刃物を取り付けられるようにされた加工機といえば、
マシニングセンタです。
(友人のいる森精機をステマしながら)
マシニングセンタは、パレットの旋回からワークの原点出し、刃物交換、加工など
全てプログラム制御された加工機で、少量多品種生産から単純な大量生産まで1台でこなす
機械加工設備のマルチロールファイターです。
もちろんお値段もそのへんの設備よりは高くなり、
コストと場所の問題からとても個人では導入できません。
で、レベルを下げていって考えてみます。
CNCフライス盤
は、その名のとおり数値制御されたフライス盤です。
こちらはマシニングセンタ等とは異なり、刃物は人間が交換するようになります。
小型のNCフライスはまだ値段が高く、
いわゆる3Dプリンタ程度のものではアルミ加工ができなくなってしまいます。
さらにレベルを落として単純なフライス盤を考えます。
ここで生じる問題は、ドリルによる穴あけ加工のみです。
そこで今回導入したのが、ドリルチャックが装備可能な小型フライス盤です。
サイズ比較のため、横にfigmaお嬢様にお立ち遊ばされていただきました。
こちらのプロクソン製フライス盤は見てのとおり小型で、
部屋のインテリアとしても秀逸です。
(部屋に展開しても大丈夫な大きさ、という意味です)
テーブル等がアルミで、精度は少しプアなところはありますが、
アルミ程度の加工も問題なくでき、ホビー用途には十分なレベルです。
6mmコレットチャックに加えてドリルチャックも装備できるため、
穴あけもそこそこの精度で行うことができます。
■ 6.効果確認
加工の前に、ネジ位置の決定をします。
使用するCADツールが変わっていますが・・・。
あとはひたすらに作っていきます。
まずは大まかに切り出した材料の両端面をエンドミルでフライス加工します。
次に、ノギスで寸法を見ながら端面を削っていき、指定の長さ寸法にします。
この段階で原点出しができるようになったので、
タップの下穴や通り穴、サーボ軸受け部の穴などを開けていきます。
通常のボール盤加工ですとポンチが必要だったりしますが、
今回はXシンニングドリルとテーブルに任せてポンチを打たず、時間を節約できました。
次にタップの下穴にタップを立ててネジ止めができるようにします。
このへんで飽きてきますので組める部品が組めるかどうか確認したりします。
あとはフレームの形状を出すために、
Vブロックやダイヤルゲージでバイスの角度出しをしながらフライス加工をします。
こうして暫定でフレーム部品が完成です。
次に一度仮組みし、サーボホーンを手で動かしたりしながら
不具合抽出を行います。
この時点で約1年経過(笑)。
コミックマーケットのわさびさんのスペースで仮の上半身が装着されました。
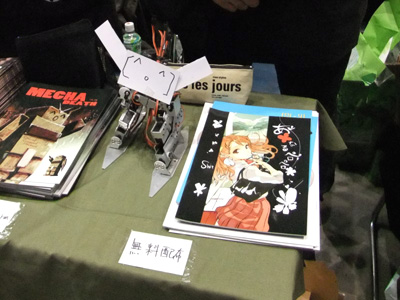
おかげさまで海外の人に写真を撮られたり、
高分子材料でロボットの外装を自作してる人、
某学校の同期の人
とお話する機会がありました。
抽出された不具合を解決したら、上半身(電池や基盤部を含む)と組み合わせて完成です。
背中の配線はこの写真を撮ったあとにまとめました・・・。
■ 7.標準化及び今後の課題
今回はフライス盤をはじめ、ある程度の工具類も揃い
ホビー加工に必要充分な環境を構築することができました。
今後の課題?
AEセンサやステッピングモータを使って
パソコンからNC制御させることができれば大幅な時間短縮と
位置補完による加工可能な形状増加が見込め、
そのための部品や技術も揃ってはいるのですが・・・
時間的な余裕がなく実施できていません。
あ、あと間に合わせなのでバランスバネは仕込めていません(笑)。
第6話は以上です。
指摘や意見がありましたら、拍手か掲示板などで
一言頂けると幸いです。
第7話では、ジャイロを使わず単純なモーション作成を予定しています。
■ past ■ up ■ future ■